Changa
Mega Poster
So, as a result of the seemingly increase in accidents involving restraints not being properly lowered to secure guests, I had an idea at random of an alternate way to sense a restraint's position & wanted to see what y'all thought regarding it's feasibility!
Using Mack restraints as an example: Each seat has a total of four non-contact proximity sensors (likely infrared due to their low cost and maintenance) mounted to both the harness and seat around the thigh area. These would measure the distance between the seat and harness from the riders' thighs, therefore determining how relatively secure they are. Eg: A rider would be stapled if the combined proximity readings of each leg is zero; if there is a gap in the harness, but it is within a threshold distance, rider's are secured while still allowing for airtime; If riders push their legs up to try and keep the lap bar high, the seat-side sensors would exceed the total distance and flag the issue. This would therefore be more representative of the rider's safety than just the closing angle of the harness.
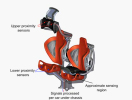
These could all be linked to a control unit on the underside of each car to interpret the respective signals from each switch. Power and data can be transferred through track-side contacts (either through bus-bars or B&M style contacts), then fed back to the operator to highlight any seat errors. In case there are any functional issues with the sensors, the operator can override a false seat error to dispatch a car if the attendants can verify the safety of the affected rider.
The main setback that I found was that rider thighs are deformable, which would skew the relative distances between the sensors and let them get away with lifting their legs to keep the lap-bar up, but could also be accounted for with other means.
What are your thoughts? Please let me know as brianstorming stuff like this is always good fun.
Using Mack restraints as an example: Each seat has a total of four non-contact proximity sensors (likely infrared due to their low cost and maintenance) mounted to both the harness and seat around the thigh area. These would measure the distance between the seat and harness from the riders' thighs, therefore determining how relatively secure they are. Eg: A rider would be stapled if the combined proximity readings of each leg is zero; if there is a gap in the harness, but it is within a threshold distance, rider's are secured while still allowing for airtime; If riders push their legs up to try and keep the lap bar high, the seat-side sensors would exceed the total distance and flag the issue. This would therefore be more representative of the rider's safety than just the closing angle of the harness.
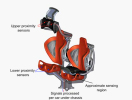
These could all be linked to a control unit on the underside of each car to interpret the respective signals from each switch. Power and data can be transferred through track-side contacts (either through bus-bars or B&M style contacts), then fed back to the operator to highlight any seat errors. In case there are any functional issues with the sensors, the operator can override a false seat error to dispatch a car if the attendants can verify the safety of the affected rider.
The main setback that I found was that rider thighs are deformable, which would skew the relative distances between the sensors and let them get away with lifting their legs to keep the lap-bar up, but could also be accounted for with other means.
What are your thoughts? Please let me know as brianstorming stuff like this is always good fun.
